Conveying technology for car washes
Reliability with MINDA engineering, where steel drag chains are replaced with plastic conveyor belts.
In car washes, vehicle rims are often damaged when the wheels get too close to the puller chains at the sides. Even in cases of significant mistracking, this is ruled out when MINDA technology with plastic conveyor belts is used. Normally, lane barriers aren’t needed at all. If they are required, they are so flat that even aluminium drop centre rims, spoilers and sport chassis don’t come into contact with them.
Vehicle conveyor belts
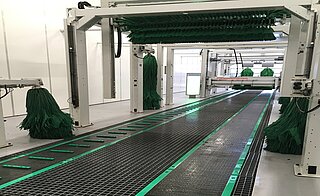
Innovative single- and double-track conveyors for car washes.
Plastic conveyor belts are ideal for:
- Conveying vehicles without damaging the rims
- Wide tyres and vehicles with lowered bodies
- Minimal risk of accidents for operatives and customers
As our concept doesn’t involve open rollers and chains running, the risk of accidents happening to operatives and customers is cut drastically.
The advantage of MINDA technology is that it’s quick to assemble and efficient to operate.
Choosing MINDA’s single- and double-track conveyors with plastic modular belts is an exceptionally reliable conveying solution and it’s practical too. Plastic conveyor belts don’t require any take-up units and only need low pit depths. This facilitates creating the foundations for new car washes and allows old ones to be converted by using existing chain shafts.
The modular design means they can be fitted in 2 days.
- Easy to retrofit
- Versatile, robust and maintenance friendly
- Excellent performance
- Customer friendly
Robust, maintenance-free design
Components subjected to a lot of wear and tear such as drive and deflection shafts are made of solid material. Chains, sprockets, grips, side guides, guide rollers etc. come in highly impact-resistant plastic and don’t require lubrication. Much less maintenance is required than for conventional drag chains.
The belt’s supporting structure consists of galvanised steel components.
Robust, maintenance-free design
Side guides, guide rollers and grips are available in different colours.
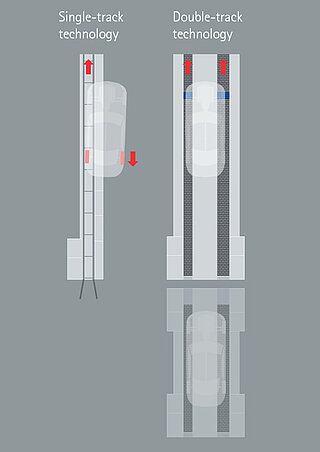
Intelligent details
Direct drive via a slip-on gear unit which replaces conventional drives with chains with a maintenance-free slip-on gear unit motor. Fits into existing chain shafts and extends the drag track by 500 mm without involving any work on foundations.
Flexible belt assembly: plastic modular belts can be fitted with wheel stoppers and grips at any position, which can be replaced or moved from above at any time. Thanks to chain links in different colours, the modular belt itself can come with clearly visible position markings.
Transfer point with continuous rollers for precise alignment when transferring from belt to belt. Centres the vehicles perfectly without interrupting the feed.
Infeed belt: for synchronised infeed of vehicles into the car wash. The safe solution for long car washes with customer viewing bays. The vehicle is driven until the front tyre is as far as it will go onto the stationary infeed belt and then all its occupants get out. The vehicle enters the car wash once the operative starts the infeed belt (e.g. after any pretreatment).
Guide roller with guide plate: can manage even the most difficult of driving manoeuvres and helps inexperienced drivers to position their vehicles. The wheel is driven onto the guide plate which can be moved sideways and is automatically moved to the right track by the guide rollers.
Double-track conveyors: MINDA’s reliable alternative
Double-track technology is the only way of guaranteeing that serious accidents (e.g. due to wheel lock-ups). Further advantages compensate for the fact that a second track needs installing because grips or lane barriers aren’t needed at all and the whole car wash can be walked on without any risk of tripping up.
Vehicles can be driven onto the car wash in the direction of travel and any gaps created beforehand closed.