Fully-automatic CLT-production
Designed for CLT elements up to a length of 18.4 m, Minda realized a customized cross laminated timber plant at the Russian customer Ladozhsky. But that was just the beginning of a successful cooperation.
Around two hours' drive east of St. Petersburg in the Leningrad region lies Avrovo, where ZAO Ladozhsky realised a large Greenfield project for the production of cross laminated timber. In the presence of high-ranking political representatives, Director General Yuri Vorobyev inaugurated the new cross laminated timber plant on 16 April 2021 and proudly demonstrated the fully automated production. Since then, production has been steadily picking up speed, which gives cause for an interim report.
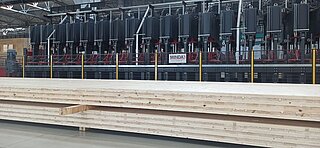
The planning on the part of Ladozhsky for the establishment of a cross laminated timber production already began several years ago. Minda, Minden/DE, only entered the planning process later and, therefore, had to develop a line concept for an already existing hall.
With 260 m by 95 m it is quite spacious, but there should also be room for more production lines. The heart of the line is a high-speed press type TimberPress 336 HS. According to Minda, the design of the press for maximum product dimensions of panels with a width up to 3.65 m and a length of 18.4 m is exceptional and currently gives ZAO Ladozhsky a unique selling point on the Russian market. The laying table with a full-surface plastic chain conveyor belonging to the press is fed by a double vacuum laying gantry, which picks up the loose cross and longitudinal layers from the preparation stations and then forms the package to be pressed on the laying table. Between the laying cycles, a 3.7 m wide glue application head applies the 1C PUR glue in one go.
Forward-looking plant concept
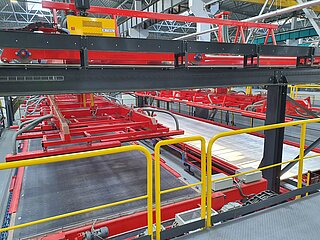
The reverse drive of the laying table makes it possible to drive back already pressed packages from the press into the laying area and then to place further layers, glue them and press them again. This system makes it possible to work with only one glue and a relatively short open time. Nevertheless, cross laminated timber panels with a large number of layers and many glue joints can be produced.
"Only this concept developed by Minda made it possible to achieve the goals in terms of plant capacity on the one hand and product variety on the other,' reports Vorobyev and adds: "The market will continue to grow, the demands on the product will increase - you have to be prepared for that.''
Accordingly, the further plant concept is also designed with foresight. Cross lamellas can be cut to size from finger-jointed lamellas via a cross-cut system and fed to the laying area - or fed into the system via a bypass as already planed panels. Vorobyev further emphasises: "The additional possibility of feeding cross-layer lamellas doubles the line capacity in the press area in one go. This means that we are no longer solely dependent on the capacity of the finger jointing line as far as the production volume is concerned”.
Further contracts with MINDA already signed
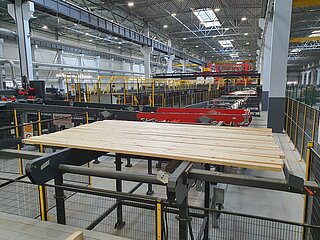
After planing the longitudinal layer lamellas are automatically collected into complete layers and prepared - however, a discharge of these lamellas with a length of up to 18.4 m into a separate hall aisle is already planned.
Vorobyev grins meaningfully and continues: "Who knows what the future will bring?" With Minda's automatic curing storage on three floors, it is at least clear what may still come: "There is still space available in the hall for three additional floors - the elevators are already designed for this," Vorobyev adds.
After the successful start of the cross laminated timber production, the general manager is now curiously looking into the future - the contracts for the delivery of a complementary production line for glulam at the same location have already been signed with Minda.