Individuelle Lösungen für den Wagenkastenbau
Der Wagenkasten bildet die äußere Hülle von Schienenfahrzeugen, die großen Einfluss auf die Sicherheit und den Komfort sowie auf Kosten und Leistungsfähigkeit hat.
Wagenkästen sind heute meist modular aufgebaut. Sie bestehen aus einzelnen Modulen/ Segmenten, die oft in Kleinserien gefertigt werden. Dabei kommen produktspezifische Vorrichtungen für das Fertigen einzelner Segmente zum Einsatz.
Aufgrund unserer jahrelangen Erfahrung entwickeln und fertigen wir Spann- und Klemmvorrichtungen, Sonderschweißvorrichtungen und diverse andere anwendungsspezifische Vorrichtungen für den Wagenkastenbau. Dabei kommen neben pneumatischer und hydraulischer auch die elektromagnetische Spanntechnik zum Einsatz.
Produktbeispiele von maßgeschneiderten Vorrichtungen für den Wagenkastenbau
Magnetische Aufspannvorrichtung für car-body-Laserschweißanlagen
Diese kundenspezifische Spannvorrichtung dient dem Laserschweißen kompletter Schienenfahrzeug-Baugruppen des Wagenkastens und bildet die äußere Fahrzeugkontur als Negativ ab. Nach dem Bestücken der Vorrichtung fährt diese schienengebunden in die Laserschweißkabine ein.
Aufbau der Vorrichtung
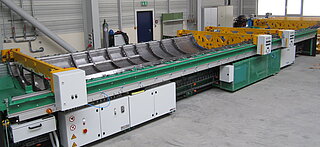
Die Vorrichtung besteht aus einem verfahrbaren Grundrahmen mit selbstständigem Antrieb. Die Bauteilauflage ist mit Magneten ausgeführt, die mittels Gruppenbildung unterschiedlich zuschaltbar sind.
In Verlängerung der Spannvorrichtung befindet sich ein sogenannter Spannbrückenbahnhof. In diesem befinden sich diverse Spannbrücken zum Positionieren, Spannen und Halten während des Heftens und Schweißens. Weitere Aufbauteile, die an der Bauteilauflage befestigt werden können, komplettieren die Vorrichtung.
Funktionsweise der Schweißvorrichtung
Alle konturgewalzten Bleche, Versteifungen und Gerippestrukturen werden elektromagnetisch, programmgesteuert gespannt. Einbauteile werden mit den Spannbrücken positioniert.
Zunächst erfolgt das Verschweißen der Dachhautbleche. Meldeleuchten signalisieren dem Bediener die Position und Anzahl der benötigten Spannbrücken zum Heften der Querträger. Anschließend werden noch weitere Teile mittels Spannbrücken und anderer Vorrichtungseinheiten positioniert, gespannt, geheftet und verschweißt.
Effizienz durch Elektro-Permanent Magneten
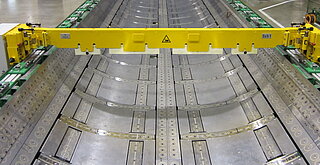
Das Spannen und Entspannen mit Elektro-Dauermagnet-Spannplatten erfolgt durch das Magnetisieren bzw. Entmagnetisieren mittels Stromstoß.
Durch Unterteilung der gesamten Spannfläche in einzelne Magnetgruppen können verschiedene Baugruppen auf derselben Vorrichtung geschweißt werden. Angepasst an die Werkstückkonturen entstehen gleichmäßig verteilt hohe Spann- und Haltekräfte.
Eine drastische Verkürzung der Rüstzeiten führt zu geringeren Stillstandszeiten und somit zur Erhöhung der Produktivität. Reduzierte Instandhaltungskosten durch geringeren Verschleiß vervollständigen die Vorteile und den daraus enstehenden Nutzen dieser Magnetspannvorrichtung.
Technische Daten
Alle Daten können kunden- bzw. anwendungsspezifisch angepasst werden.
Abmessungen der Vorrichtung: | Gesamthöhe: | ca. 1.250 mm |
Gesamtbreite: | ca. 3.000 mm | |
Gesamtlänge: | ca. 15.350 mm | |
Gewichtt: | ca. 22.000 kg | |
Anzahl der Fahrantriebe: | 2 | |
Anzahl der Spannbrücken: | 9 |
Nutzen/ Vorteile
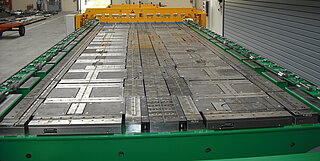
- Positionier- u. Spannprozesse erfolgen automatisch
- sauberes Fügen der Profile (Schweißspalt "0")
- geringe Umrüst- und Einrichtzeiten
- hohe Wiederholgenauigkeit
- hohe Prozesssicherheit
- für verschiedene Varianten verwendbar
Universalschweißvorrichtung für Seitenwände
Diese kundenspezifische Schweißvorrichtung dient dem Ausrichten, Fügen, Fixieren und Positionieren von ebenen oder gewölbten Profilen für das Schweißen von Seitenwänden von Fernverkehrszügen.
Aufbau der Spann- und Schweißvorrichtung
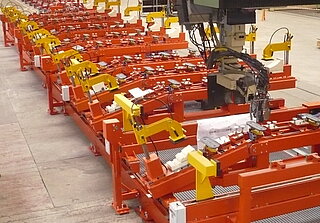
Das ca. 24 m lange Grundgestell ist im Baukastensystem stabil und geteilt ausgeführt. Es besteht aus mehreren Segmenten, die miteinander verschraubt sind.
Entlang der Längsträger befinden sich verstellbare Aufnahmemöglichkeiten für die Aufnahme, Längsverschiebung und Arretierung der Querträger. Zur Vorrichtung gehören 10 Quertraversen und 7 Fügevorrichtungen.
Weitere Bestandteile der Schweißvorrichtung sind 4 Wendeeinrichtungen, die für das Drehen der Baugruppe benötigt werden. Anschläge und diverses Zubehör komplettieren die Vorrichtung.
Zwischen den Grundgestell-Längsträgern ist das Grundgestell mit Gitterrosten ausgelegt, so dass eine erhöhte Arbeitsplattform zur Umrüstung entsteht.
Funktionsweise der Spann- und Schweißvorrichtung
Für jede zu fertigende Seitenwandvariante gibt es definierte Positionen für die Fügevorrichtungen und Quertraversen. Diese werden zu Beginn eingestellt. Dazu sind am Grundrahmen Schilder angebracht, auf denen die jeweilige Position für den Seitenwandtypen abzulesen ist. Markierungen erleichtern das Ausrichten.
Die einzelnen Profile werden in die entsprechenden Fügeeinrichtungen und Quertraversen eingelegt, ausgerichtet und gespannt. Anschließend erfolgt durch die Roboteranlage das Verschweißen der Vorderseite.
Nach dem Schweißen der Vorderseite wird die Baugruppe mit der Wendevorrichtung gedreht. Dann kann auch das Verschweißen der Rückseite erfolgen.
Technische Daten
Alle Daten können kunden- bzw. anwendungsspezifisch angepasst werden.
Abmessungen: | Länge: | 26.170 mm |
Breite: | 4.980 mm | |
Höhe: | 2.350 mm | |
Auflagenhöhe: | 1.362 mm | |
Zugkräfte: | 40 Vakuumspanner | |
60 Spannzylinder | ||
20 Hydraulikzylinder | ||
Druckkräfte: | Spannzylinder | |
Hydraulikzylinder |
Nutzen/ Vorteile
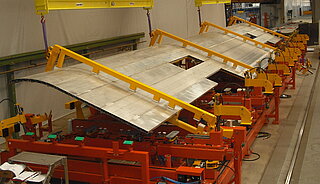
- für verschiedene Wagentypen einsetzbar
- Positionier-, Füge- und Spannprozesse erfolgen programmgesteuert
- sauberes Fügen der Profile ("Schweißspalt "0")
- geringe Umrüst- und Einrichtzeiten
- hohe Wiederholgenauigkeit
- hohe Prozesssicherheit
- hohe Wartungsfreundlichkeit
- einfache Reinigungsmöglichkeit
Schweißvorrichtungssystem für Seitenwände
In dieser kundenspezifischen Schweißvorrichtung können zwei Seitenwände zu je ca. 20 m hintereinander aufgelegt werden. Die aus Alu-Profilen zusammengeschweißten Seitenwände werden mit vorgefertigten Türteilen bzw. -baugruppen komplettiert.
Alle Auflageböcke sind über die gesamte Vorrichtungslänge in y-Richtung verfahr- und arretierbar. Dadurch wird eine Neukonfiguration der Vorrichtung möglich, um kurzfristig auch andere Seitenwandtypen zu bearbeiten.
Das Auflegen erfolgt im geraden Konturbereich. Die Auflagen ermöglichen die erforderliche Ebenheit ohne aufwendige Nachstellvorgänge. Nach dem Auflegen der Seitenwände werden die Spannelemente aus der hängenden Lage über der Seitenwand abgesteckt.
Baugruppen der Sondervorrichtung
- Grundgestell mit seitlicher Fahrschiene und Arbeitsplattform aus Gitterrosten
- 8 Einzelböcke mit je 2 Horizontalspindeln für die Vorsprengung
- 4 Doppelböcke mit Zwischenpodest
Technische Daten
Alle Daten können kunden- bzw. anwendungsspezifisch angepasst werden.
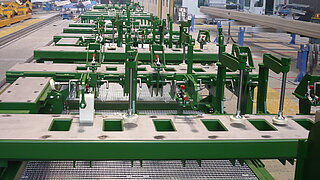
Abmessungen:
Länge: 40.000 mm
Breite: 2.330 mm
Höhe: 1.030 mm
Nutzen/ Vorteile
- für verschiedene Seitenwandtypen einsetzbar
- geringe Umrüst- und Einrichtzeiten
- hohe Wiederholgenauigkeit
- hohe Prozesssicherheit
Weitere MINDA-Lösungen für den Sektor Bahntechnik
Drehgestell- und Radsatzhandling
Unsere Dienstleistungen und Bereiche:
Anwendungsspezifische Vorrichtungen und Anlagen
Unsere Dienstleistungen und Bereiche: