MINDA for DS Smith Austria: Umbau während des laufenden Produktionsbetriebes
Bei der DS Smith Packaging Austria GmbH, Margarethen am Moos, hat MINDA die Automatisierung des Zwischenlagers und eine neue Palettensicherungslinie mit Palettenbeladezentrum und zwei neuen Umreifungslinien umgesetzt. Wie dieses Projekt bei laufendem Produktionsbetrieb gelingen konnte? Lesen Sie mehr in unserer Success Story:

Projektplanung als Schlüssel
Im Vorfeld war eine intensive Planung notwendig, um trotz großflächiger Umbaumaßnahmen sicherzustellen, dass es keinen Produktionsausfall im Werk gibt. “Es wurde sehr akribisch geplant, welche Bauschritte wir wann durchführen. Es sind viele Projektschritte gleichzeitig passiert und die Einhaltung des Zeitplans war essentiell. Das konnte mit Hilfe des sorgfältig durchdachten Montageplans von MINDA gelingen.”, erklärt Patrick Baldauf, Site Operational Excellence Lead und Projektleiter bei DS Smith Packaging Austria. “Durch die Anschlusspläne von MINDA konnten wir Vorarbeiten wie Kabelwege und Zuleitungen bereits im Vorfeld gut lösen.”, ergänzt Florian Pointinger, Maintenance & Engineering Manager.
“Auf die exzellente Projektvorbereitung bei DS Smith konnten wir uns verlassen, das matchte einfach!”, bestätigt Bianca Böke, Vertrieb und Projektleitung MINDA.
Die überholten Komponenten wurden komplett demontiert und erneuert, um Prozesssicherheit für die Zukunft sicherzustellen: „Alles auf dem aktuellen Stand zu haben ist eine große Erleichterung.“, sagt Pointinger.
Innerhalb der Palettensicherungslinie wurden zwei alte Aggregate ohne Produktionsausfälle gegen eine neue Palettenbeladestation BoP (Block on Pallet) getauscht: “Das Werk durfte nicht stillstehen. Das Tagesgeschäft musste weiterlaufen.”, so Baldauf.
So wurden beispielsweise die Schienen des Transferwagens zum Abtransport der Stapel aus der Wellpappenerzeugungsanlage (WPA) ins Zwischenlager während des laufenden Betriebs erneuert. Die neuen Schienen mit einer geänderten Spurweite wurden gefräst, verlegt und vergossen, während der alte Transferwagen auf den bisherigen Schienen weiterfahren konnte. Im Anschluss wurde der alte Transferwagen in einem Zug durch den neuen ersetzt, der auf den vorgearbeiteten Schienen umgehend wieder eingesetzt werden konnte: “Es waren oft kleine Schritte in der Planung, die aber einen riesigen Effekt auf das gesamte Projekt hatten!”, erinnert sich Baldauf.
Ziel des Projektes war es, durch Automatisierung und das Einbringen neuer Komponenten, eine noch bessere Performance im Werk zu erzielen und sowohl die Transporteigenschaften als auch die Stapelbilder zu optimieren.
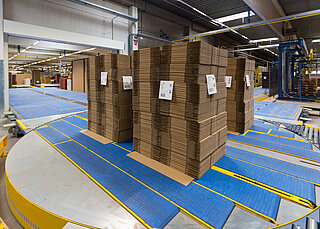
WPA-Abtransport und Maschinenzuführung
Der Bereich vor den Verarbeitungsmaschinen inklusive Zwischenlager wurde voll automatisiert. Die Materialflussverfolgung ist nun ab der Wellpappenanlage gegeben. Damit ist jeder Stapel jederzeit im Werk visualisiert und identifizierbar.
In der Maschinenperipherie setzt DS Smith auf die MINDA-Advector-Familie als Prefeeder und die Nutzentrennerlinie Fractor in Kooperation mit MuK (Maschinenbau und Konstruktion GmbH Elmshorn).
Durch die Automatisierung des Werkes gibt es zentrale Benefits in den täglichen Arbeitsabläufen. So gestaltet sich beispielsweise die Planung im Vorfeld leichter und auch Liefertouren im Versand können besser koordiniert werden: “Früher waren Rundgänge durch die Produktion notwendig, heute kann der Materialfluss am Bildschirm verfolgt werden, um optimal zu planen.”, bemerkt Baldauf.
Auch auf die Qualitätssicherung hat das Projekt Einfluss genommen: Vor der Automatisierung waren Handeingriffe notwendig und durch deren Wegfall ließ sich die Reklamationsquote durch Bedienerfehler reduzieren, da nun eine lückenlose computergesteuerte Erfassung möglich ist.
Im Zwischenlager wurden nichtangetriebene Rollenbahnen durch Kunststoffkettenförderer ersetzt. Durch Vermeidung des Sheet-Walk-Effects (“Elefantenfuß”) wird nicht nur die Qualität der Stapel signifikant erhöht, sondern auch ein Beitrag zur Nachhaltigkeit durch weniger Ausschuss geleistet. Ebenso stand die Erhöhung der Bedienersicherheit bei der Wahl der Kunststoffketten im Vordergrund.
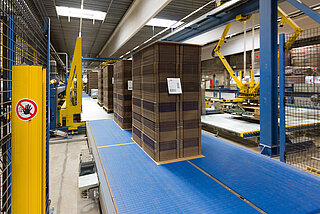
Fertigwarenbereich und Palettenbeladezentrum
Die Maschinenentsorgungslinien wurden so modifiziert, dass der Transferwagen diese mit seinen beiden Decks parallel entsorgen kann und somit eine Leistungssteigerung erzielt werden konnte.
Das Layout der Versandhalle wurde komplett angepasst. Statt wie zuvor über zwei Beladelinien zu palettieren, wird jetzt die komplette Fertigware über eine Beladestation und zwei Umreifungsanlagen für den Versand vorbereitet. Die Palettensicherungslinie ist für den optimalen Materialfluss angepasst, sodass die Stapel zentralisiert an einem Punkt nahe dem Versand- und Fertigwarenlager abgenommen werden.
Um die neue Palettensicherungslinie zu planen, hat MINDA auf einen 3D-Scan im Vorfeld gesetzt. “Dieser Scan war essentiell für die die weitere Umsetzung.”, betont Baldauf.
Die 360° umfassenden Scans ermöglichten eine detailgetreue Visualisierung des Werkes und sorgten für maximale Planungssicherheit und Kollisionskontrolle im Vorfeld. So konnten beispielsweise bauliche Gegebenheiten wie Deckenbinder, Sprinkler und Beleuchtungsanlagen in der Versandhalle direkt identifiziert werden.
Die Stapel aus der Verarbeitungshalle werden über eine Drehscheibe mit zwei separaten Decks der Palettensicherungslinie zugeführt, so dass bis zu vier Stapel gleichzeitig gedreht werden können. Stapel, die für die Palettierung noch die Orientierung verändern müssen, werden über eine Winkelübergabe Richtung Beladestation transportiert.
Auf der Pufferstrecke vor der Palettenbeladestation können mehrere Blöcke vorgehalten werden, sodass ein kontinuierlicher Durchfluss gewährleistet wird.
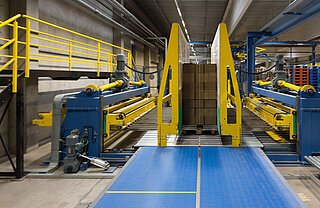
Palettenbeladestation BoP
Mit der neuen Installation wird die Leistung mit nur einer Palettenbeladestation erreicht. Damit kann auch das Bedienpersonal effizienter eingesetzt werden. Im Fokus steht dabei keine Stellenreduktion, sondern die Mitarbeiter durch Vorantreiben der Automatisierung auch auf qualifiziertere Aufgaben umzuschulen.
Innerhalb der Doppelbeladestation für Format- oder Fertigware, kann beispielsweise ein großformatiger Block auf Palettenbilder gesetzt werden oder es können zwei Blöcke kleinerer Formate in gleicher Breite innerhalb eines Arbeitszyklus palettiert werden.
Ebenfalls zu berücksichtigen war die Zugänglichkeit zur Beladestation für die Bediener, sodass diese nicht den Staplerverkehr kreuzen. Um diese Sicherheit zu gewährleisten, wurde ein Podest errichtet, welches den Laufweg über eine Brücke an der Beladestation ermöglicht. Dies gehört zum Planungs- und Lieferumfang der Firma MINDA.
Bei der Layout-Optimierung hat MINDA stets die gesamtheitliche Planung für den Kunden im Blick. So entstehen intelligente Layoutentwicklungen zum Beispiel auch für kundenspezifische Fluchtweg-Planungen.
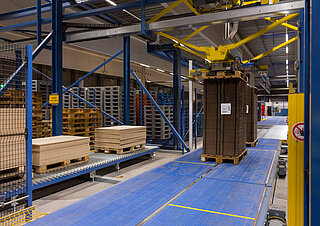
Deckmaterialaufleger und Umreifungslinien
Dem Materialfluss folgend wurde nach der Palettenbeladestation ein neuer Deckmaterialaufleger installiert. Dieser ist für das Auflegen der Kopfpaletten oder Abdeckplatten zuständig. Die Installation erforderte aufgrund der Gebäudegegebenheiten, bezüglich der Deckenbinder, eine kundenspezifische Konstruktion.
Die Palettenstapel werden durch einen Wender für Leerpaletten passend bereitgestellt, sodass sie gleich richtig abgenommen und aufgelegt werden. Zur Performancesteigerung, und um die Prozesssicherheit zu gewährleisten, wird die Fertigware nach dem Auflegen des Deckmaterials per Shuttle auf zwei Umreifungslinien verteilt.
Im Sinne der Nachhaltigkeit wurden vor Ort viele guterhaltene bereits vorhandene Komponenten wiederverwendet und in die neue Steuerung integriert. Neben Umreifungsmaschinen sind auch Stretch-Wickler in die Fertigwarenlinie eingebunden.
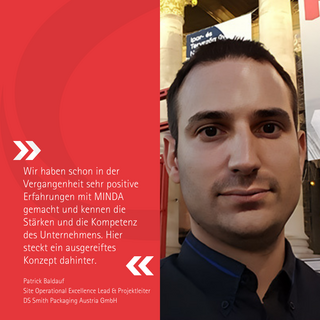
Performance durch Automatisierung
Durch die zielgerichtete Vorbereitung und Zusammenarbeit der Projektleitungsteams konnten die Neuerungen während des laufenden Betriebes umgesetzt werden.
Ausschlaggebend war die Planung im Vorfeld, die insbesondere durch einen passgenauen Montageplan seitens MINDA visualisiert wurde. “Der Montageplan war für unsere Personalplanung entscheidend.”, ergänzt Pointinger. Auch wenn ein Maintenance-Team vorhanden sei, durfte das Tagesgeschäft durch den großflächigen Umbau nicht vernachlässigt werden.
“Es ist eine Mammutaufgabe so ein Projekt zu planen. Durch die Montageplanung konnten alle Vorarbeiten unsererseits reibungslos laufen und etwaige Engpässe bereits im Vorfeld entschärft werden.”, so Baldauf.
Das Endergebnis bestätigt Baldauf bei der Wahl von MINDA als Partner für die komplette Automatisierung des Werkes: “Wir haben schon in der Vergangenheit sehr positive Erfahrungen mit MINDA gemacht und kennen die Stärken und die Kompetenz des Unternehmens. Hier steckt ein ausgereiftes Konzept dahinter."
„Auch die Zuverlässigkeit wartungsarmer Komponenten und die gezielte Unterstützung durch die MINDA Servicetechniker im Bedarfsfall sind für uns überzeugend“, ergänzt Pointinger.
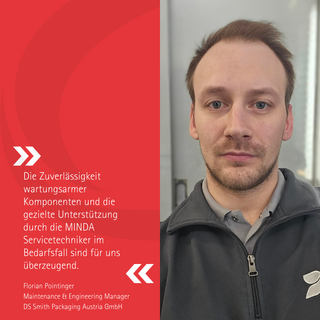
Was für ein spannendes Projekt, bei dem durch intelligente Layoutplanung, Automatisierung der Komponenten und Upgrade des gesamten Steuerungssystems für zukunftssichere Prozesssicherheit bei optimiertem Materialfluss gesorgt wurde!
„Auf einer Baustelle muss man oft schnelle Entscheidungen treffen, aber gute! Und das komplette Team von MINDA, jeder einzelne Monteur und Techniker, der hier war, hat uns sehr gut unterstützt. Die waren alle top!“, erinnert sich Pointinger.
Mit einem Lächeln im Gesicht ergänzt Baldauf: “Das war für mich die längste Montagezeit in meiner Karriere. Und so sehr ich das komplette MINDA-Team vor Ort auch ins Herz geschlossen hatte, ich war auch froh, als sie wieder gegangen sind. Dass dann Schluss war!”
... und das waren wir ehrlich gesagt auch! Denn wir freuen uns immer, die Projekte erfolgreich zum Abschluss zu bringen. Aber das heißt noch lange nicht, dass für die Zukunft Schluss ist! Ganz im Gegenteil – wir freuen uns bereits jetzt auf weitere gemeinsame Projekte mit der DS Smith Packaging Austria GmbH!