Customized concept for storage solutions
MINDA implemented three individual storage solutions under production conditions in the existing plant at MODEL AG in Weinfelden
Model AG - based in Switzerland - and MINDA have a long-standing partnership. “We decided for MINDA because in our plant we already had two MINDA loading stations for finished goods and the discharge of sheet goods from the corrugator,” explains Thomas Weibel, Project Manager at Model AG in Weinfelden. In a joint next step, the gap from the corrugator to the converting machines was automated to achieve an even more efficient production process. In addition, an in-house storage, a three-level storage and an area storage were installed. In this step, the discharge from the corrugator to the converting machines was designed without pallets to minimize both dirt and waste - caused by damage to the lowest sheets on the pallets: “The complete transport process of the sheets with pallets and forklift traffic is eliminated, saving around 8% in personnel costs. In addition, we have less damage to the infrastructure and the sheet goods,” adds Weibel.
Conversion in existing buildings as a special challenge
In three existing production halls with different roof structures and heights, it was intended directly from the start of the planning process not to change this structure. In order to reach an optimum automation of the supply of the converting machines according to the spatial conditions, each machine hall was considered separately based on its individual requirements (including the output of the corrugator and the input of the converting machines). MINDA developed an overall solution concept for Model with three different storage types, consisting of in-house storage (shelf storage system), three-level storage and area storage.
This is where Thomas Weibel considers the biggest challenges of the joint project: “The main challenge was certainly the conversion during ongoing production, which required great flexibility in terms of temporary solutions with mutual understanding for our production as well as for MINDA. Another challenge was the preparation of the master data in our ERP system.”
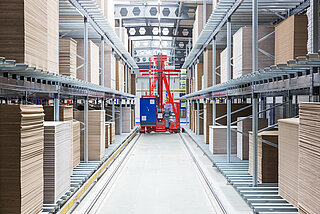
In-house storage
An in-house storage, consisting of the steel structure of the rack and one storage and retrieval machine per aisle, with four aisles was directly connected to the corrugator. The open design of the rack, which only needed to be fenced and not completely enclosed, creates optimal conditions for intermediate storage of the corrugated board. By storing the stacks in the in-house storage, the conditions of the corrugated board are homogenized. Another advantage of this storage solution is the access to every single stack due to the single-deep storage. As a result, the utilization of the storage area in the in-house storage is higher and the transfer of stock is much more efficient. Capacity and utilization of the storage area are optimally coordinated.
The height of the warehouse was adapted to the existing hall structure and designed on three levels. Storage in the 3-level warehouse is done without pallets and, moreover, the stacking height of the compartments was optimized for Model. Thus, individual stacking dimensions can be assigned to individual compartments, depending on existing interfering contours of the ceiling pattern, to achieve an optimum use of the available space. The individual compartments can be occupied by blocks of different widths, so that, for example, a large block or even two small half widths can be stored in one compartment.
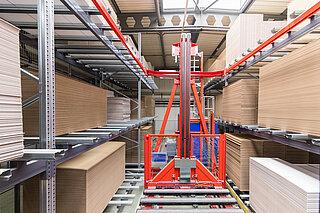
MINDA's specially designed storage and retrieval machines (SRM) only have two bottom rails and do not require an upper guidance. They supply the compartments in both directions by telescopic forks. Due to the enclosure of the SRM and the ultra-modern safety technology used by MINDA, the storage and retrieval machines do not present any risk to the operator.
The use of an in-house storage is ideal when space is limited, as this storage system is built vertically upwards on a small footprint, making maximum use of the given hall height. In addition, it offers the advantage that the rack structure itself requires little maintenance, so that no spare parts need to be kept for the rack. Usually, industrial floor is sufficient for the construction of an in-house storage and no additional foundations are required.
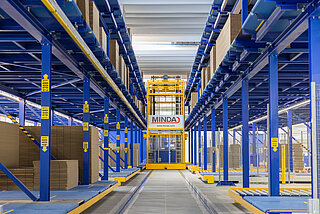
Three-level storage
The three-level storage designed by MINDA is also adapted to the existing hall height and the storage areas on the first and second floor overbuild the machine feeding lines with the conveyor lengths of the plastic chain conveyors, so that a three-level storage optimally utilizes the available free space "similar to a balcony". The warehouse is designed as an area storage with driven conveyors.
Order changes can be implemented very quickly, as the order lines are already pre-sorted in the warehouse and are prepared for quicker access. The implemented storage solution corresponds to the high processing speed of the inliners.
Depending on the machine, stacks of different widths are processed. The different widths are also considered for the storage in the three-level warehouse, as side-by-side plastic chain conveyors in the warehouse can be controlled individually or coupled to make optimum use of the available storage area depending on the width of the orders.
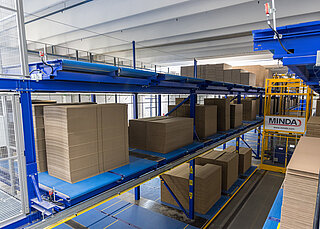
This means that storage lines of different widths are always considered in the machine storage. The plastic chain conveyors on the first and second floor are integrated in the steel structure. Both elements were designed and supplied by MINDA from a single source. The gentle transport of goods on the integrated plastic chain conveyors avoids the "sheet walk effect" and thus damage of the stacks during storage process.
To optimize the use of space, the storage was built on the 1st and 2nd floor above the machine infeed.
Stairs at the front of the warehouse ensure that each level can be accessed at any time, so that fast access is possible in the event of possible malfunctions. In addition, the storage is operated as a LiFo (last in - first out) warehouse on the first and second level.
The installed three-deck transfer car provides the storage on both sides with material, performing superimposed travel and lifting operations to increase productivity.
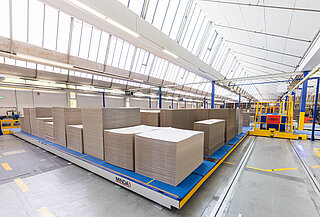
Area storage
MINDA has supplemented the storage concept for Model in this area with an additional area storage in front of the die-cutting machines. Given the low ceiling height, it was not necessary to build a multi-level storage in front of the die-cutting machines for capacity reasons.
In the area storage, the stacks are sorted by order. Individual control of the plastic chain conveyors allows stacks of different widths to be stored. The plastic chain conveyors can be individually adjusted to the stack width by single, double, or triple coupling, so that different order widths and lengths can be stored depending on the application. The coupling of the plastic chain conveyors in the area storage led to the optimum space utilization.
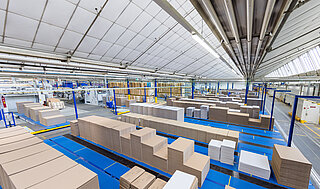
To achieve the best possible use of the available space, the stacks in this storage type are stored without gaps. In addition, the integrated plastic chain conveyors prevent the sheet walk effect.
The machine operators can already evaluate the stacks in advance according to flatness and flute alignment and, if necessary, carry out a rotation (180°, 90°, -90°) within the machine infeed by means of a turning device.
To be prepared for the future, MINDA left free space for the later installation of larger machine parts in the sector of the area storage.
Close cooperation
Model AG and MINDA jointly accepted the challenge of implementing the automation in existing halls and during ongoing production and worked closely together to achieve the common goal: “The cooperation was always very constructive and targeted. Challenges were openly communicated,” says Thomas Weibel.
With the interaction of in-house, three-level and area storage, the production process in front of the converting machines was optimally automated, in different designs, with a comprehensive solution concept.
And further projects with MINDA are already being implemented: “Currently we are planning the supply and discharge of the two new printing machines (EFI Nozomi digital printing machine, König und Bauer, Chroma XPro 7 color flexo printing machines) which will be installed this summer,” adds Weibel.
We are already looking forward to this and other joint projects!
Model AG
With 784 employees Model AG is the leading packaging manufacturer in Switzerland with three production sites and is managed by Daniel and Elisabeth Model in the fourth generation. Model develops, produces and supplies intelligent, innovative and high-quality display and packaging solutions made of corrugated and solid board all over the company group in Switzerland, Germany, the Czech Republic, Poland, Austria, Croatia and Slovakia. Click here for the website: https://www.modelgroup.com/