Production lines for engineered wood products
Engineered Wood Products - At MINDA, we attach great importance to partnership-based cooperation in all project phases. Our tailor-made production lines for engineered wood products are characterized by resource efficiency, reliability, high performance and a high degree of automation.
In addition to planning and solution finding for customer-specific tasks, the complete package also includes engineering, production including in-house tests, installation and commissioning, training of operating personnel and optimization of the line through to after-sales service.
Egger Holzwerkstoffe in St. Johann/Austria wanted to achieve a greater added value for the solid wood and OSB products being produced. They had developed a new resource-saving, dimensionally stable and accurate product, the EcoBox. To manufacture this product on a suitable production line, they contacted us as a plant and press specialist.
Preparations for the development of a new production line for the Egger EcoBox
The search for a partner was preceded by a market analysis to determine Egger's requirements.
At an initial meeting between Egger and MINDA, the newly developed product and its requirements were presented. The results of a preliminary market analysis with the expected production volumes for an initial layout of a production plant were also discussed in detail.
The Egger project team included Project Manager Josef Gasteiger and Product Manager Arne Lüdemann. From MINDA Sales Manager Andreas Rudolf, Technology Consultant Dietmar Wilde and Project Manager Jonas Keller from MINDA were present.
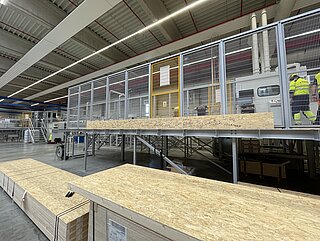
What could such a line for producing the EcoBox look like?
MINDA's team developed a solution for a fully automated high-performance line within a very short time. MINDA also presented a solution for launching a prototype line with lower requirements in terms of performance and degree of automation.
At the same time, the costs for the different line types were determined.
To determine the line performance, calculations based on experience were carried out and assumptions made. To confirm these assumptions, a sample station was built providing information on the time in which certain operations could be carried out. Additional glue and press tests followed.
After just a few workshops, the solution for the pilot line was ready. As no site decision had been made at this point, planning was carried out “on a greenfield site”.
Once Egger had decided on the Wismar site in an existing hall, MINDA adapted the concept of the pilot line to the existing hall conditions.
It only took a few months from the idea to the line concept up to the readiness for order placing.
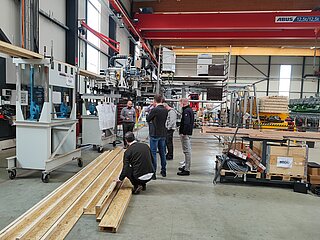
MINDA optimized the work processes during the construction of the individual assembly groups.
With a focus on the relationship between personnel costs and the degree of automation, individual items were automated.
After initial calculations and tests, the required line performance was even exceeded without any additional effort or costs.
To ensure a reliable and well-founded line design, various test series were carried out at the start of order processing under MINDA’s direction. These included tests on joining, the composition of press fillings and a determination of the gluing time and process time. These findings formed the basis for the individual process sequences.
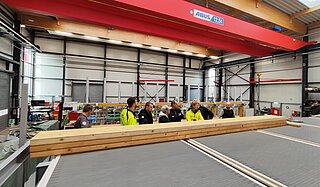
Successful performance run
At the end of September 2024, the time had come. Production of the EcoBox was running at full speed and nothing stood in the way of a performance run.
The line worked perfectly during the two-day performance run, meaning that the close cooperation between EGGER and MINDA enabled the promised performance to be significantly exceeded. A great success. The agreed shift performance was achieved in less than 7 hours.
MINDA’s Project Manager Jonas Keller took responsibility right from the start, coordinating many details and reacting quickly to changes. He coordinated the engineering and production at the MINDA sites as well as the supply from external partners. He mastered this project brilliantly and was happy about the successful acceptance of the line. He thanked everyone involved for the very successful collaboration.
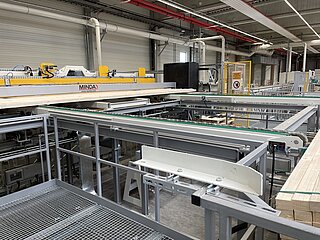
Recipe for success: open and honest social interaction
Egger’s Project Manager Josef Gasteiger was full of praise for the MINDA team after the performance run. He spoke of a: “More than successful production of the EcoBox, which went very well according to the agreed specifications.”
He was not the only one with words of praise, but he also expressed his thanks on behalf of EGGER, in particular to the technical/production plant management, production management, product management and the project supervisors/participants on site. “BEST THANKS for the good cooperation and the implementation!” he said.
Josef Gasteiger continued: “I think we have all learned a lot, even though we had tight deadlines right from the start. However, WE have now achieved a BIG milestone TOGETHER and that after just 3 months of commissioning.”
The project manager summarized the cooperation with MINDA as follows: “In addition to the human factor, I believe that the recipe for success are such partners who are open and honest, make quick decisions in certain project phases, keep their word and seal this with a handshake!”
“....and what is really important was the fact that we often had fun together.”
The family business Egger Holzwerkstoffe
WE MAKE MORE OUT OF WOOD
The EGGER Group, with headquarters in St. Johann in Tirol, is one of the leading international manufacturers of wood-based materials. The family-owned company, founded in 1961, today produces at 22 locations in 11 countries worldwide with more than 11,000 employees. Its customers are the furniture industry, specialist wood retailers, DIY markets and DIY stores. Sustainable management lies at the heart of EGGER's corporate DNA. And this has been the case since the company was founded, because even then Fritz Egger senior considered wood far too valuable to simply throw it away.