In-house Storage (IHS)
In-house storages are compact storage solutions that can be integrated into existing space conditions. An efficient solution is given starting from a hall height of 10 m. The stacks of corrugated cardboard to be stored can be stored without pallets or in the finished goods area also on pallets.
These in-house storages can consist of several aisles. A storage and retrieval machine operates in each aisle; its telescopic forks can work in the rack in both directions. The storage usually takes place by single- or double-deep storage. This means that the block can be reached at any time. Multi-deep storage in the shelves with smaller stack widths is possible.
Inhouse storage as a compact storage solution
As a result of the rapid progress at the processing plant of Janmar Centrum, a fully automatic transport system was installed and a fully automatic MINDA in-house storage system was integrated into an existing hall.
The combination of a rigid in-house storage system with a dynamic area storage system achieves an optimal balance of large storage space and high flexibility.
Plastic chain conveyor In-house Storage
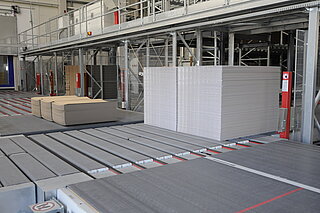
Advantages:
- Gentle transport and avoidance of damage
- Transport of all qualities and formats processed
- Transport without „sheet walk effect“
- Smooth transport through frequency-controlled drives
- Reverse operation mode
- Clean, easy-care surface
- Low maintenance expenses
- High safety for the operating personnel
- Complete visualization and material flow tracking
Turntable
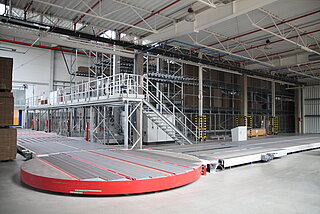
The transport direction can be changed by 90° or any other angle by means of turntables.
Right angle stations
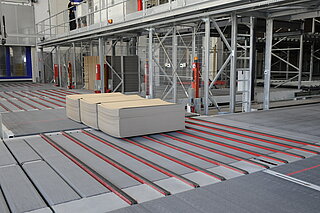
Right angle stations are used in corrugated cardboard transport systems when the transport direction in the process is changed by 90° and thus the length-width-ratio is also changed.
Advantages:
- Both transport directions with plastic chain
- Large-scale support of goods
- Gentle transport of bottom sheets
- Suitable for all formats and qualities
- Compact and safe construction
Vertical lift
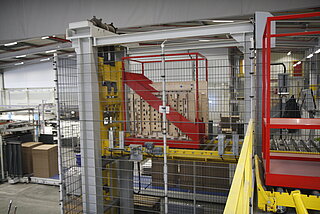
Vertical lifts connect two or more levels in order to return tools, printing plates and colors back into the warehouse. They can also be used for heavy piece goods.
Advantages:
- Low maintenance compared to cable elevators
- Execution with or without conveyor technology
- High lifting and lowering speeds
- No pit required
- Increased safety by two lifting belts each
- Lean, space-saving construction
Double-floor intermediate storage
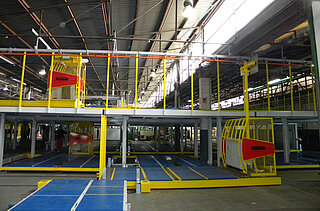
Application:
- when there is not enough space on one floor
- safe discharge from one or serveral corrugators for all sizes and speeds
- continuous supply of all machines for further processing and a direct line for articles for sale
- gentle fully-automatic stack transport
- reduction of waste material
- increased production by intelligent material flow control
Advantages:
- space-saving, optimal utilization of space especially regarding the height of the hall
- high throughput
- possibility of resorting from stage to stage or from floor to floor
- electrical lifting devices on transfer car
- camera monitoring of top floor
- simple and efficient protection of double-floor storage
- utilization of other floors to store printing plates, colours and tools
Control
Complex control of individual intralogistics systems
There is a complex control process behind the flexibility and the size of these intralogistics processes. This process also includes software solutions optimally adjusted to the individual conditions.
They are based on MINDA MoveIT, the control and visualization system for intralogistics programmed by MINDA.
The system coodinates the control of transport sections, floor conveyors and packing devices according to the plans of the ERP system.
This superordinated control based on PC is further internally developed by experienced programmers.
MINDA MoveIT guarantees a fully-automatic operation in all transport sections. The transport operations are optimized so that all storing places are efficiently used.
In the discharge area behind the corrugator the system exactly defines how and in which order and sequence the corrugated cardboard stacks reach the intermediate storage and the converting machines with an optimal utilization of the transport capacity.
These calculations are effected in real time and are the condition for continuous new evaluations of the prioritites of the individual operations.
Complete transport operation
The converting machines are supplied in time with goods for conversion according to the definitions of the ERP systems. After the conversion, the corrugated cardboard stacks are discharged from the machines and fed to the pallet protection. (picture 2) Here the correct pallet type is automatically prepared and the data for the strapping are available. The secured goods reach the finished goods storage and are ready for despatch.
The system flexibly reacts to inputs by the operators. During the entire production process the products can always be identified.
A dynamic visualization of the processes provides the customer an overview of the complete production flow.
Further MINDA solutions for the corrugated board industry.
Machine feeding
Our services and fields:
Finished goods transport
Our services and fields: