Maßgeschneiderte Lösungen bis ins Detail
Sie finden keine passende Anlage für Ihre Arbeitsaufgaben? Dann sind wir der richtige Ansprechpartner! Wir fertigen nichts „von der Stange“, wir realisieren Ihre Wünsche.
Mit unserer umfassenden Fachkenntnis und langjährigen Erfahrung entwickeln und realisieren wir maßgeschneiderte Lösungen; angefangen von Transport- und Anbindungstechnik, über Roboterapplikationen bis hin zu komplexen Handlingsaufgaben.
Alles aus einer Hand – unser Leistungspaket bietet Ihnen alles von der Entwicklung über die Realisierung bis hin zum After-Sales.
Transportsystem für Feuerfeststeine
In diesem Anwendungsfall wurde ein automatisches Transportsystem für Feuerfeststeine (von der Steinpresse bis zur Aufstapelung auf die Versandpalette) individuell für den Kunden konzipiert.
Prinzipieller Aufbau der Anlage
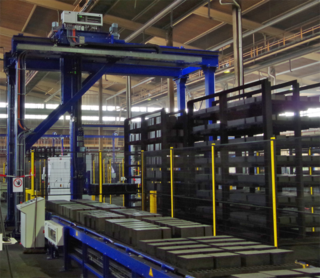
1. Hordentransport
1.1 Hordentransport mit Tauchnockenförderern und Kettentransfer mit Magnetgreifer
1.2 Automatische Querverschiebbühnen (Transferwagen)
2. Palettierstrecke
2.1 Entladeportal für Spezialsteine-Paletten
2.2 Kettenförderer mit Einführungsblechen zum Ausrichten
2.3 Angetriebene Rollenbahnen als Förder- und Pufferstrecken
2.4 Handabsetzstelle: angetriebene Rollenbahn mit Hubtisch
2.5 Leerpalettenmagazin
2.6 Hubtisch mit Schwerlastrollenförderern
2.7 Winkelübergabe
1. Funktionsweise Hordenwagentransport
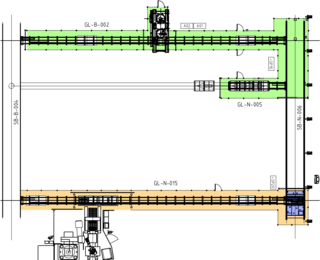
Die Steine befinden sich nach der Steinpresse auf Spezialpaletten, die wiederum in Hordenwagen gestapelt werden.
Die Kettentransfereinheit mit Magnetkupplung dient dem Transport der bis zu 12 t schweren Hordenwagen. Der Kettentransfer ist neben der Transportstrecke aufgebaut, der Mitnahmeschlitten ist für eine seitliche Mitnahme modifiziert.
Bei dieser Lösung haben wir die im Bereich der Fördertechnik bewährte Technik der Kettentransfereinheit mit unseren Erfahrungen bei der Magnetspanntechnik im Bereich Schweißvorrichtungen erfolgreich kombiniert.
Die Querverschiebewagen sind schienengebunden und transportieren bzw. verteilen sowohl die leeren als auch die vollen Hordenwagen auf die unterschiedlichen Prozessstrecken. Zum Aufnehmen und Abgeben der Hordenwagen werden Schubeinheiten verwendet.
Vorteile dieser Lösung
- Magnetgreifeinheit ermöglicht Abholen des Hordenwagens aus ungenauer Startposition
- Millimetergenaue Feinpositionierung
- wartungsarm
- funktioniert auch in verschmutzter Umgebung
2. Funktionsweise der Palettierstrecke
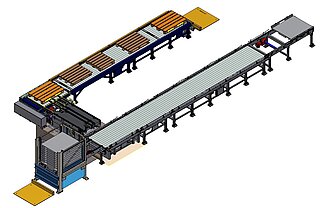
Mit dem Entladeportal erfolgt das automatische Entladen der Hordenwagen von unten nach oben. Das Portal kann waagerecht und in der Höhe verfahren werden. Durch das Drehen der Gabeln am Portal werden die Paletten auf dem Kettenförderer abgesetzt. Eine angetriebene Rollenbahn (dient auch als Pufferstrecke) übernimmt die volle Palette und führt diese der Handabsatzstelle zu.
Die angetriebene Rollenbahn am Handabsetzplatz ist auf einem Hubtisch platziert, damit die Entnahmehöhe angepasst werden kann. Der Arbeitsplatz ist mit einer Vakuum-Hebehilfe ausgestattet, um die schweren Steine ergonomisch zu bewegen. Die Steine werden so auf eine Verkaufspalette gestapelt, die sich auf dem Hubtisch mit Schwerlastrollenförderer befindet. Durch definiertes Absenken des Hubtisches können die Steine in mehreren Lagen übereinander auf der Verkaufspalette gestapelt werden.
Der Abtransport der leeren Spezial-Palette in das Palettenmagazin erfolgt auf Tastendruck. Die beladene Verkaufspalette wird dann weiter zur Winkelübergabe transportiert.
Die Winkelübergabe transportiert die Verkaufspalette um 90° gedreht auf die Abtransportstrecke.
Technische Daten
Transportlänge (gesamt): ca. 50 m
max. Gewicht pro Hordenwagen: 12 t
max. Gewicht Verkaufspalette: 2 t
Bearbeitungsstrecke für Betonrohre
Über diese Anlage können alle Arbeitsschritte nach dem Tempern der Betonrohre realisiert werden. Für Betonrohre mit unterschiedlichen Durchmessern kann so der Transport, das definierte Kippen der Rohre, das Aufrauen der Rohrenden sowie das Reinigen und Kennzeichnen automatisch erfolgen.
In die Anlage eingebunden ist ein automatisches Palettenhandling.
Kundennutzen
- Vielzahl von Teilarbeitsgängen sind vollautomatisiert miteinander verkettet
- Transport und Handling verschiedenster Querschnitte
- Inklusive Handhabungstechnik
- SPS-Steuerung und Produktverfolgung
- Anlage ist erweiterbar
Funktionsweise
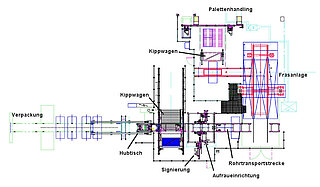
Alle Rohre werden senkrecht, auf bis zu vier Paletten, stehend aus dem Tempertunnel von einem Kippwagen mit Vakuumsaugern und Rollenförderer abgenommen. Durch Kippen des Wagens werden die Rohre quer liegend auf die Förderstrecke zum Fräsportal abgegeben.
Die Paletten verbleiben dabei angesaugt am Wagen. Nach Zurückkippen werden die Paletten von den Saugeinheiten freigegeben, gegen einen Anschlag gefahren und von einem Portal mit Vakuumgreifern entnommen und an einen definierten Platz gestapelt.
Besonderheiten/ Kundennutzen
- Fallen der Paletten in den Fangbereich des Kippwagens wird verhindert
- sensorische Überwachung der Palettenplätze
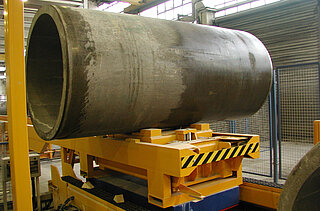
Die Übernahme der Betonrohre von der Fräsanlage erfolgt mittels Transportwagen. Dieser Transportwagen, der mit einem Hubtisch ausgestattet ist, transportiert die Rohre auf einer feststehenden Transportstrecke zur Endbearbeitung.
Dabei gibt der Transportwagen das Rohr an eine Rollvorrichtung ab, die dem Drehen der Rohre bei den weiteren Bearbeitungsschritten dient.
Besonderheit
- Der Achsabstand der Rollen ist elektromotorisch auf den Rohrtyp und Rohrdurchmesser einstellbar.
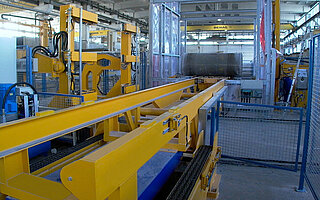
Die Endbearbeitung erfolgt in 3 Arbeitsschritten:
1. Aufrauen: Mittels Fräswerkzeuge, die pneumatisch an das Rohr herangeführt und angedrückt werden, erfolgt an beiden Seiten des Rohres ein Aufrauen. Somit wird ein späteres Verkleben an diesen Stellen ermöglicht.
2. Waschen: Die Wascheinheit befindet sich an einer horizontal und vertikal verfahrbaren Lineareinheit und dient der Reinigung der zu bedruckenden Bereiche.
3. Signieren: Verbliebene Wassertropfen werden abgeblasen. Der Druckkopf befindet sich an einer Lineareinheit und kann in horizontaler und vertikaler Richtung verfahren werden.
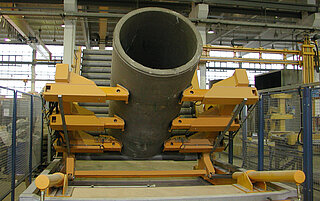
Beim Abtransport der Rohre werden zwei Ziele unterschieden:
1. Der Transportwagen befördert das Rohr auf einen Schwerlast-Kettenförderer, der das Rohr zu einem weiteren Verarbeitungsschritt transportiert.
2. Der Transportwagen übergibt das Rohr an einen weiteren Kippwagen, der mit Haltearmen das Rohr aufnimmt. Das Rohr wird aufgerichtet und kann mittels Hallenkran abgenommen werden.
Förderstrecke für Formen- und Trockenroste
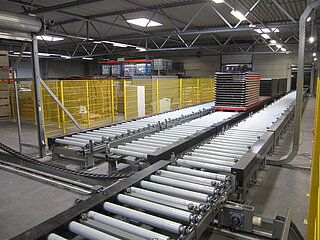
Formen und Trockenroste werden bei der Herstellung von Leicht- und Betonplatten benötigt. Da die Anzahl und die Varianten immer größer wurden, bekam die Lagerung und Pufferung sowie der automatisierte Umlauf eine große Bedeutung.
Die Formen und Trockenroste werden übereinander gestellt und in Stapeln transportiert, gepuffert und gelagert. Durch entsprechende Auslegung der Förderstrecke wurden so eine Umlaufmöglichkeit der Stapel und die Möglichkeit einer Vorsortierung erreicht.
Eine Anlage besteht aus 35 Rollenförderern (aufgeteilt in mehrere Linien) für den Speicherumlauf sowie der bedarfsgerechten Bereitstellung und 3 schienengebundenen Fahrwagen für den Austausch mit den Fertigungslinien. Dabei werden die Formen vereinzelt auf einen Kettenförderer gesetzt, der diese dann in den weiteren Prozess befördert. In einem zusätzlichen Bereich wurde zu einem späteren Zeitpunkt weitere 21 Rollenförderer ( in 3 Linien) und ein Transferwagen installiert, um die Zuführung und die Lagerung von Formenstapeln zu gewährleisten. Ein Portal zum Vereinzeln bzw. Stapeln komplettiert die Gesamtanlage.
Sowohl funktionell als auch daten- und steuerungstechnisch sind diese Bereiche in das Gesamtkonzept des Werkes eingebunden.
Der gesamte Bereich ist als Sicherheitsbereich abgegrenzt.
Technische Daten
Parameter | Rollenförderer | Transferwagen | Kettenförderer |
Länge | ca. 3.300/ 6.500 mm | ca. 3.300 mm | 3.800 mm |
Breite | ca. 1.270 mm | ca. 1.300/ 2.300 mm | 1.585 mm |
Höhe | ca. 600 mm | ca. 600/ 1.300 mm | 966 mm |
Tragfähigkeit | 10 t | 10 t | 500 kg |
Antrieb | 0,75 kW | 2,2 kW | 0,55 kW |
Transportstrecke für Plattenformen und Transportrahmen
Um die Fertigungskapazitäten von Trockenbauelementen beim Kunden zu erhöhen, war die Integration einer neuen Fertigungsstrecke in einer bestehenden Bausubstanz erforderlich. Aufgrund der geringen Platzverhältnisse stellte die transporttechnische Erweiterung eine Herausforderung dar.
Die automatische Versorgung der Fertigungsstrecke mit Plattenformen, die auf einem Transportrahmen gestapelt sin, musste gewährleistet werden. Zum einen werden die leeren Formen einzeln abgestapelt und dem Fertigungsbereich zugeführt und zum anderen müssen dann die leeren Transportrahmen zurückgeführt werden.
Funktionsweise
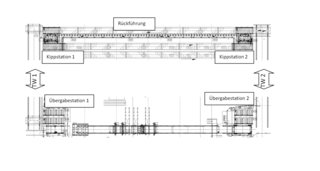
1. Zuführung leerer Formen
Ein Verfahrwagen (TW1) bringt den Formenstapel auf einem Transportrahmen zum Übergabeplatz 1 (Anfang der Fertigungsstrecke). Dort entnimmt ein Portalgreifer einzelne Formen und setzt diese auf einen Kettenförderer ab, der sie dann weiter zum Befüllen transportiert.
Die gefüllten Formen werden bis zum Übergabeplatz 2 mittels Kettenförderer transportiert und dort mit einem weiteren Portalgreifer wieder auf einen Transportrahmen gestapelt. Der Transferwagen (TW2) bringt dann den Formenstapel zur nächsten Bearbeitungsstation.
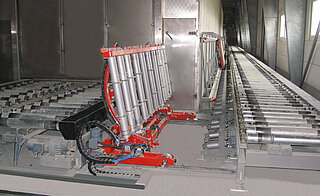
2. Rückführung Transportrahmen
Der Verfahrwagen TW1 bringt die leeren Transportrahmen nach dem Abstapeln zur Kippstation 1. Der Kippwagen ist eine Sonderkonstruktion, die es ermöglicht, den Transportrahmen um ca. 80° zu drehen und diesen dann an eine senkrechte Stützrollenbahn (Neigung ca. 80°) abzugeben.
Am Ende der Rückführstrecke steht ein zweiter Kippwagen, der den Transportrahmen aufnimmt und wieder in die waagerechte Lage zurückdreht. Der Transferwagen TW2 befördert die Rahmen zu ihrem weiteren Verwendungsort.
Besonderheit
Mit dieser Lösung für die Rückführung kann der ca. 30 m lange Längstransport auf engstem Raum realisiert werden.
Förderstrecke für MDF-Plattenstapel
Um die Kapazitäten in der MDF-Plattenherstellung schrittweise zu steigern, war es erforderlich, die vorhandene Logistik für die zukünftigen Leistungsparameter anzupassen. Ziel war es, ausreichende Transportkapazitäten, einschließlich einer Pufferstrecke, zur Verfügung zu stellen und Transporte somit nicht mehr mittels Krantechnik befördern zu müssen.
Die Umsetzung der neuen Förderstrecke musste dabei ohne größere bauliche Veränderungen erfolgen. Da die neue Strecke ein Lückenschluss darstellte, musste die neue Anlage auch an die vorhandenen Systeme hinsichtlich Arbeitshöhen und Übergabegeschwindigkeiten modifiziert werden.
Funktionsweise
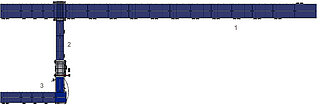
MDF-Stapel werden mittels Verfahrwagen (Transferwagen) von zwei separaten Fertigungsstrecken aufgenommen und zur neuen Förderstrecke transportiert. Die Förderstrecke übernimmt die Stapel und transportiert diese dann weiter bis zur Abzweigung. Anhand von übergebenen Daten wird entweder der Stapel weitertransportiert oder über die Winkelübergabe umgelenkt in den Bereich 2.
Die verbliebenen Stapel auf der Förderstrecke 1 werden von einem weiteren Transferwagen einer weiteren Verarbeitung zugeführt.
Die Förderstrecke 1 besteht aus insgesamt ca. 90 m Kunststoffkettenförderern und einer Winkelübergabe, die sowohl mit Kunststoffkettenförderer und einem 4-strängigen Kettenförderer für die Querverschiebung ausgestattet ist.
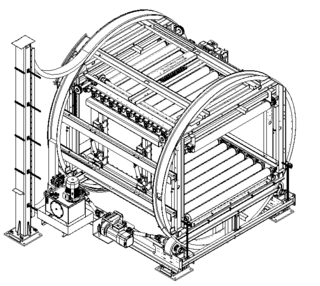
Im Bereich 2 nach der Winkelübergabe werden die Stapel ebenfalls über Kunststoffkettenförderer dem Stapelwender zugeführt. Wenn anhand der übergebenen Daten gefordert, wird im Wender der MDF-Stapel um 180° gedreht.
Der Wender ist mit zwei Rollenbahnen in der Wendetrommel ausgestattet, wobei die eine Rollenbahn höhenverstellbar ist.
Der Stapel wird in den Wender transportiert, dort mittels der Rollenbahnen geklemmt und in 2 Schritten gedreht, damit die einzelnen Platten des Stapels durch Nachrutschen ausgerichtet werden können.
Nach dem Wenden wird der Stapel wieder freigegeben und an einen Schwenkwagen dem Bereich 3 übergeben.
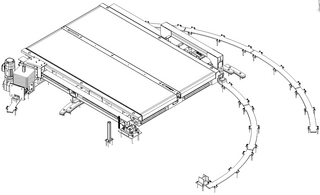
Im Abtransportbereich 3 wird nach dem Wenden der Stapel an den schienengeführten Schwenkwagen übergeben.
Dieser Schwenkwagen ist ebenfalls mit einem Kunststoffkettenförderer ausgestattet. Mittels dieses Wagens wird der MDF-Stapel dann auf weitere Kunststoffkettenförderer übergeben.
Ein weiterer Transferwagen (Querverschiebewagen) übernimmt die Stapel dann von den Förderern und transportiert sie dann in einen weiteren Verarbeitungsbereich.
Besonderheit
Die Komponenten dieser Anlage sind größtenteils kundenindividuelle Sonderkonstruktionen für den Schwerlasttransport.
Es erfolgt durch die Kunststoffkettenförderer ein ruckfreier sowie sicherer und ruhiger Lauf zum schonenden Stapeltransport. Dadurch wird kann ein Stapelversatz, der sogenannte "Elefantenfuß" vermieden werden.
Technische Daten
Parameter | Kunststoffkettenförderer | Winkelübergabe | Stapelwender | Schwenkwagen |
Länge: | 3.200 bis ca. 6.400 mm | 3.800 mm | 3.700 mm | 3.350 mm |
Breite: | ca. 3.100 mm | 4.200 mm | 3.800 mm | 3.620 mm |
Höhe: | -------- | -------- | 4.600 mm | -------- |
Arbeitshöhe: | 400 mm | 400 mm | 440 mm | 440 mm |
Tragfähigkeit: | 8 bis 15 t | 8 t | ca. 8 t | ca. 8 t |
Antrieb Förderer | 3 kW frequenzgeregelt | 3 kW frequenzgeregelt | 1,5 kW frequenzgeregelt | 3 kW frequenzgeregelt |
Drehantrieb: | -------- | -------- | 7,5 kW | -------- |
Schwenkantrieb: | -------- | -------- | -------- | 2,2 kW frequenzgeregelt |
Further MINDA solutions for building and insulation industry
Beispiele für realisierte Anlagen
Unsere Dienstleistungen und Bereiche: