Glulam (GLT) plants
For more than 40 years we have been planning and supplying customised installations to produce glued laminated timber (glulam) worldwide.
In addition to the customary material handling system and conveyor technology, our product portfolio includes a wide range of hydraulic glulam presses. Both the glulam presses and the conveyor technology for boards, lamellas and glulam beams are almost infinitely scalable. In the field of engineered timber construction, we thus implement installations for considerably large glulam beams of up to a length of 50 m, but also highly efficient and highly automated production lines for straight standard glulam beams of up to a length of 18 m.
Depending on the requirements, we plan our line technology customised in existing buildings as well as in greenfield projects. Upon request, we can integrate a wide range of third-party machines into the overall concept.
Especially in flexible production lines for order-based production - batch size 1 - our higher-level production control technology FlowMate is used. It provides the PLC controllers just-in-time with the necessary production data and ensures an efficient and continuous production. The entire line, including all third-party machines, is controlled.
Glulam production in Russia
This glulam production was designed as an addition to an already existing production line. The customer was looking for a possibility to press both 18 m long glulam and 600 mm wide LVL strips into solid supports of 600 mm x 300 mm. As these were only small series, the personnel and space requirements as well as the investment sum should be kept to a minimum.
The solution was a solid chain conveyor for the provision of the lamellas resp. LVL strips to be pressed, from where the planer with a working width of 600 mm was to be automatically fed. Via a movable roller conveyor behind the planer, glued lamellas as well as finished goods can now leave in two tracks. The glued lamellas resp. LVL strips are automatically fed into the pressing machine TimberPress T120 pro. It is equipped with an integrated packaging so that the press package is formed automatically. In the press chamber (length: 18,000 mm, height: 2,000 mm, width: 600 mm), both large LVL supports (600 mm x 300 mm) and glulam beams with a minimum width of only 100 mm can be pressed. The pressing pressure is adjusted according to the width of the component. At a maximum width of 600 mm, 1.1 N/mm² is possible.
The integrated automatic discharge in length direction behind pressing enables an immediate reloading of the press chamber and thus ensures comparatively high production quantities.
During the pressing time, the finished product can be fed again to the planer via the supply chain conveyor, which now serves as the finish planer. Behind the planer exit, the finished product is pushed out via the clean track of the roller conveyor in the conveying direction but not towards the press but to the opposite side onto a roller rail buffer for removal.
The compact system is operated by only one employee plus a forklift truck driver or crane operator. Depending on the dimensions, between 5,000 m³ and 30,000 m³ can be produced per year and shift.
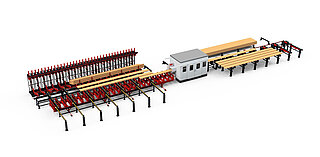
and planer feeding
and planer feeding
Location: Russia
Space requirements: 52 x 20 m
Starting material: Lamellas from veneer laminated wood
Finished product: Straight laminated beams
Length: 8,000 – 18,000 mm
Width: 100 x 600 mm
Thickness: 100 - 300 mm
Press technology: TimberPress T 120 pro
Glue: MUF
Batch size: Small series
Legend:
1. Feeding chain conveyor and planer feeding
2. Planer
3. Glue application system MUF
4. Double roller conveyor for glued lamellas and finished goods
5. TimberPress T120 pro with integrated packaging, width of press chamber 600 mm, pressing pressure 1,1 N/mm² at maximum width
6. Roller blocks for automatic discharge
Glulam and solid construction timber production in Germany
Together with our customer, we developed a flexible and efficient U-shaped glulam and solid construction timber line. The line produces 11,000 m³ of straight and curved glulam beams per year up to a maximum length of 45 metres. Here up to five types of wood are processed and sometimes are glued together to form hybrid beams.
The stacks of boards coming out of the drying system are destacked layer by layer via a vacuum destacker and the boards are separated. In addition to the moisture content of the boards, the stability is also determined. An operator assesses the visual requirements. The marked defects are then cut. A robot placed in front of the cross-cut saw sorts the lamellas quickly and reliably by surface quality, stability and wood type. The sorting into quality classes enables an optimal use of the raw wood resources.
The lamellas coming from a compact finger jointing line dry out in a curing storage, which can be divided for beam lengths up to 20 m and can be used efficiently in block operation. An automatic warehouse management system ensures that the raw material is provided from the quality class warehouse for further processing according to the individual production requirements.
Afterwards, the lamellas are glued on a horizontal press to straight or curved glulam beams being used in hall construction, timber engineering and bridge construction.
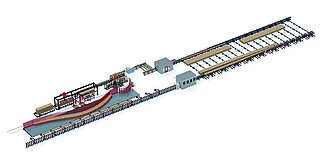
Location: Germany
Space requirement: 115 x 25 m
Starting material: unplaned panels
Finished product: curved and straight glued beams
Length: 6,000 – 45,000 mm
Width: 80 x 300 mm
Thickness: 1,350 - 2,500 mm
Press technology: TimberPress C 500
Glue: MUF
Batch size: production to order
Legend:
1. Vacuum destacker: destacking and lamella separation for sorting station
2. Quality assessment
3. Quality class warehouse: Lamella buffering in front of finger jointing line
4. Finger jointing line: Gluing to endless lamellas
5. Block curing storage: Curing of finger joints
6. Lamella planer
7. Glue application and packaging
8. TimberPress C 500: Semi-automatic pressing of curved beams
Vacuum destacker
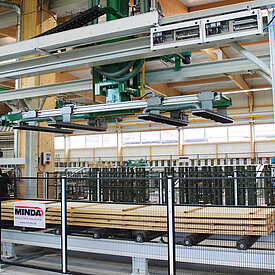
Quality assessment
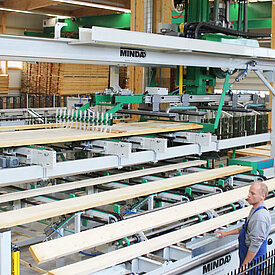
Quality sorting by robot
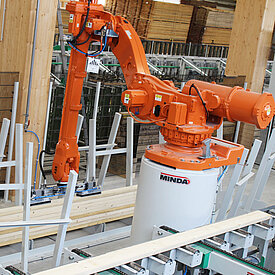
Block curing storage
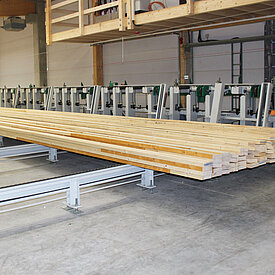
Destacking from the curing storage
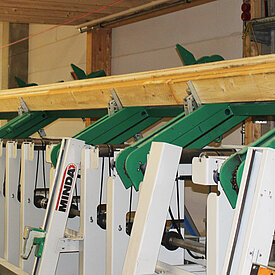
Packaging of BSH packages
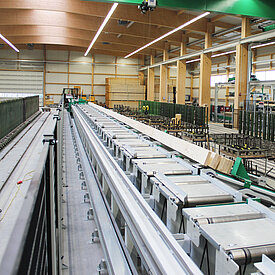