Flexible and efficient high-bay warehouse for batch size 1 on smallest area
Flexibility and automation are indispensable for a modern GLT, CLT or solid structural timber production. A fast and economical production of smallest batch sizes is the goal, no matter if it is glulam, duo, triolam, structural timber, cross laminated timber or boards.
MINDA offers individual solutions for different tasks depending on the requirements.
The high-bay warehouse systems can be integrated into a new building or into an existing one.
Our product portfolio comprises both stationary and mobile storage and retrieval units - the optimum solution for every application in the field of glued engineered timber products. This allows a production and commissioning of orders with batch size 1 in an efficient and fully automatic way.
The heart of the plant is the MINDA FlowMate control and visualization system including the warehouse managment module.
High-bay warehouse with stationary storage and retrieval unit
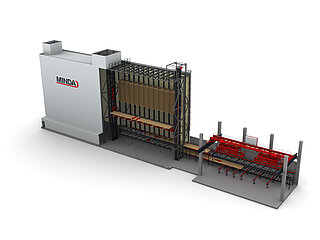
for forming the commissions
lifting system with integrated telescopic forks for storage and retrieval of the commissions
for forming the commissions
lifting system with integrated telescopic forks for storage and retrieval of the commissions
Technical data:
Suitable for the following products:
GLT, Duo-Lam, Trio-Lam, solid structural timber, CLT, boards
Component length: 2 - 22 m, individually divisible
Component width: up to 3.60 m
Component weight: up to 12 t
Total storage height: up to 36 m
Low-maintenance, compact and energy-saving system
Further designs on request!
Legend:
1. Storage in the high-bay warehouse
2. Double vertical lifter - lifting system with integrated telescopic forks for storage and retrieval of the commissions
3. First high-bay warehouse
4. Second high-bay warehouse
5. Retrieval from the high-bay warehouse
6. Vacuum portal for forming the commissions
Best possible space utilization in the high-bay warehouse
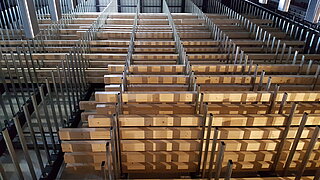
For a high storage capacity, the storage compartment heights are optimally matched with the product range. The components are flexibly stored in the storage compartments in terms of depth and length so that the available storage space is utilized in the best possible way. In length direction, several, shorter components can also be stored and retrieved next to each other - of course with single access.
Telescopic forks are used to load and unload the high-bay warehouse from both sides.
A modern drive concept ensures very low energy consumption.
Depending on the design, a load capacity of up to 12 t and an effective stroke of up to 36 m can be realized.
High-bay warehouse in skeleton structure during the construction phase
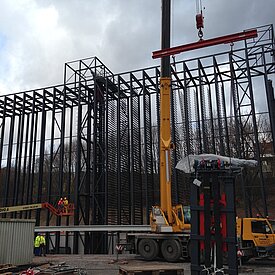
Covered high-bay warehouse
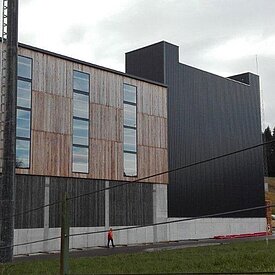
Double vertical lifter with telescopic forks
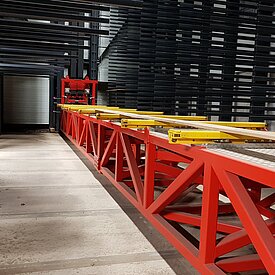
Storage of boards into the storage compartments
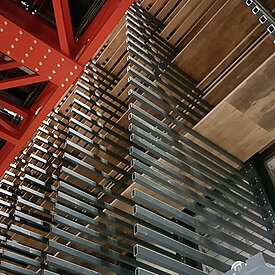
Mobile storage and retrieval unit
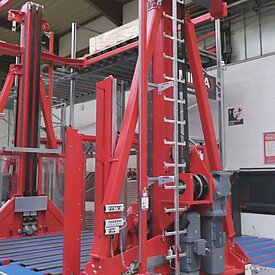