Conveyor technology for GLT, CLT as well as stacks, boards and lamellas
We are the specialists for fully automatic material transport for CLT, GLT and solid structural timber systems.
From the manipulation of dried lumber stacks to board transport or the transport of intermediate products and finished goods, our modular transport system includes all components for your individual plant.
We transport stacks and boards up to a length of 6.30 m just as reliably as lamellas up to a length of 50 m or stacks with a weight up to 17,000 kg.
In the finished goods sector, we offer solutions for small, customized components as well as for large-format CLT boards up to a width of 2.60 m or 6 m and a length of 20 m.
Conveyor technology for transport of stacks, boards and lamellas
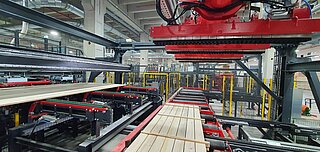
Our transport construction kit is designed for minimum and maximum dimensions of stacks/boards/lamellas, feed speeds, and cycle rates encountered in the production of glued wood building products.
In this way, we realize plants with very different performance classes - from the entry-level solution to the high-performance plant, we offer you the optimum execution.
We automate the raw material supply according to your requirements with an individual degree of automation either with forklifts or fully automatically from a high-bay warehouse.
We process stacks with and without stabilization/drying bars.
Efficient raw material logistics also includes the removal of residual stacks.
Automatic destacking is performed at different cycle rates.
We manipulate boards and lamellas in any direction, lengthwise, crosswise and vertically.
We realize compact, user-friendly complete systems for you and adapt them to your existing buildings in an optimum way.
Technical data:
Stack length: 2.4 – 6.3 m
Stack width: 1.2 – 2.4 m
Stack height: up to 5.0 m
Stack weight: up to 17 t
Board length: 2.4 – 6.3 m
Lamella length: 6.0 – 50 m
Examples of mechanizations for the transport of stacks, boards and lamellas
Curved conveyor
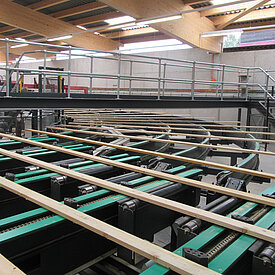
Heavy-duty stack transport and lifting unit
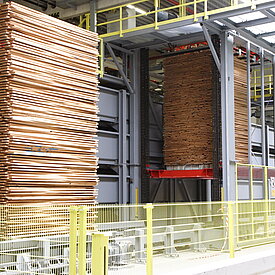
Block warehouse for finger-jointed lamellas
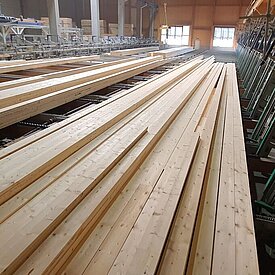
Multi-level warehouse
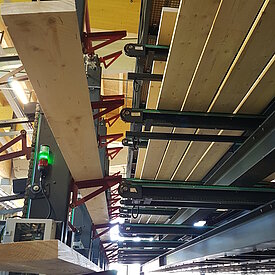
Feeding of a finger jointing line incl. scanner
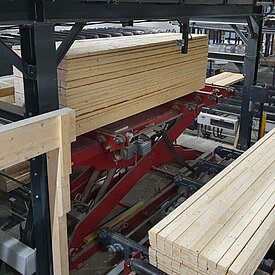
Lamella transport
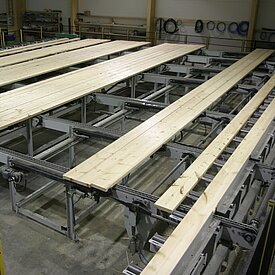
Sorting line for boards
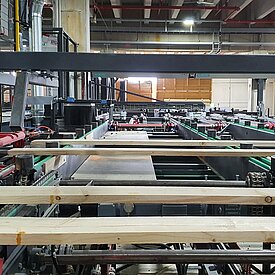
Quality sorting with robot
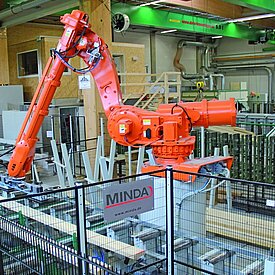
Tilt destacking
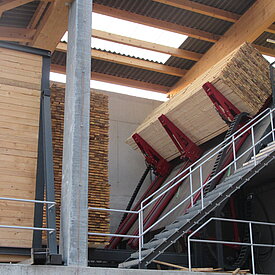
Multi-level warehouse for lamella curing
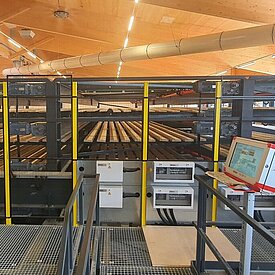
Lamella destacking from the block warehouse
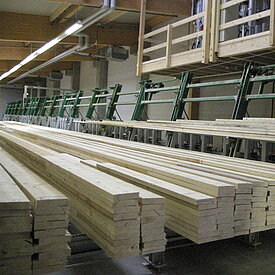
Servo-controlled planer feeding
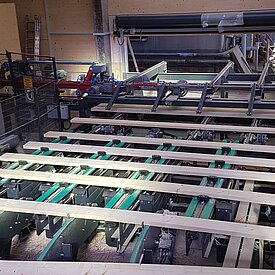
Conveyor technology for glulam (GLT) and solid structural timber
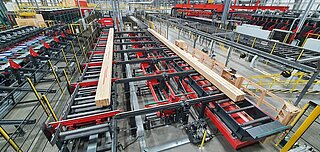
From the pressed blank to the packed, customized produced individual part, from the smallest solid structural timber cross-section to the block-glued XXL glulam beam - with our conveyor technology solutions, we feed and discharge the finishing machines such as
- Planers
- Quality control stations (repair station)
- Crosscut saws
- Stacking and packaging equipment.
Upon demand, we store the components in an order picking warehouse, which can be designed as a high-bay warehouse and an area warehouse.
Technical data:
Component length: up to 50 m
Component width: up to 2,600 mm
Component thickness: up to 800 mm
Examples of mechanizations for the transport of glulam (GLT) and solid structural timber production lines
Separation of GLT semi-finished products in front of crosscut saw
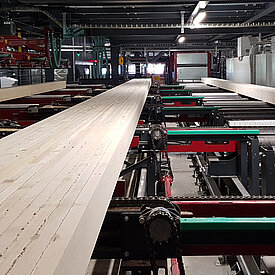
Stacking of GLT semi-finished products
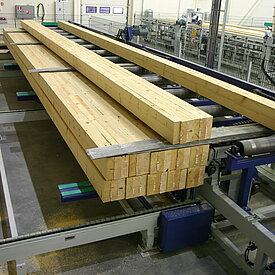
Commissioning and package formation with vacuum traverse
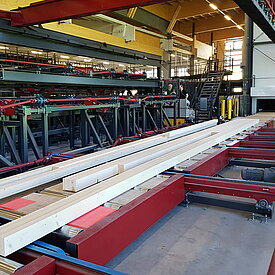
Package formation of glued lamellas before the pressing operation
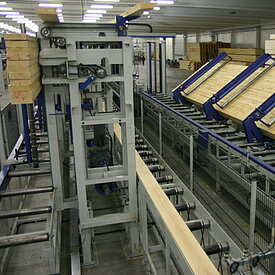
Feeding of a band saw
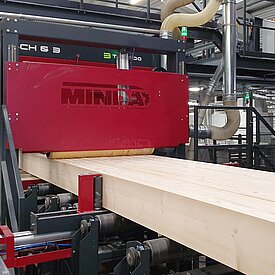
Quality inspection over two floors in cross direction
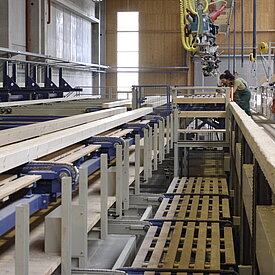
Separation of pressed GLT bars
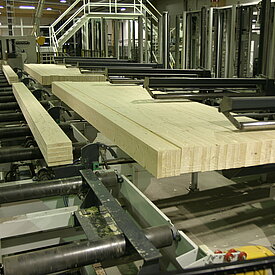
Separation of press packages and feeding of the finish planer
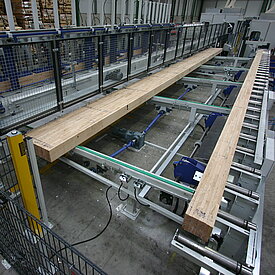
Beam saw for GLT
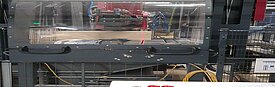
Intermediate buffering of GLT bars
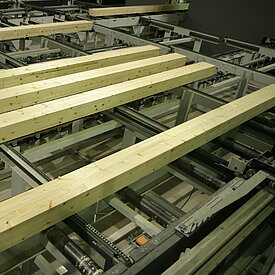
Feeding of a movable GLT press
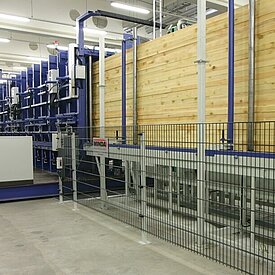
Integration of a foil wrapping machine
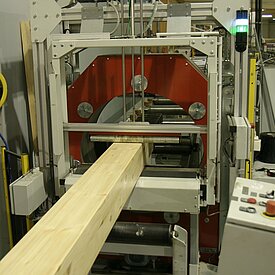
Conveyor technology for cross laminated timber (CLT)
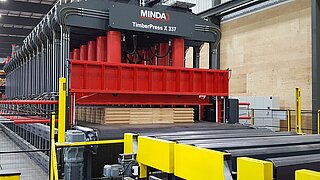
We reliably transport the CLT boards behind the cross-laminated timber press to the subsequent processing machines such as
- Sanding machines
- Joinery machines.
We also have available proven solutions for a change of floor - e.g. from the first floor to the upper floor. Of course, we take over the formatted wall and ceiling components after finishing and transport them gently to the loading area or store them in an order picking warehouse.
Technical data:
Board length: up to 20 m
Board width: up to 6 m
Board thickness: up to 400 mm
Examples of mechanizations for the transport of CLT production lines
Laying table in front of the CLT press
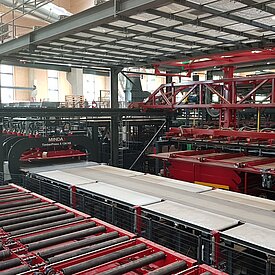
Feeding of the sanding machines for CLT elements
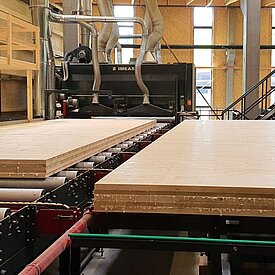
Vacuum portal for alternate laying of length and cross layers
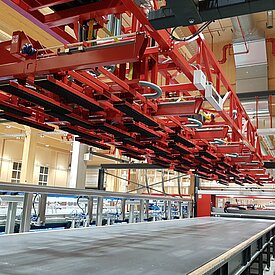
Discharge of the pressed CLT element
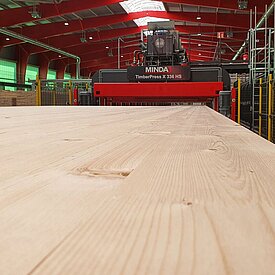
Supply of length layers
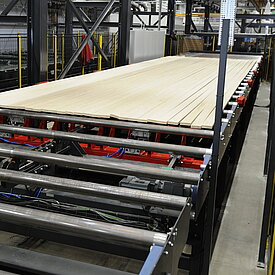
Supply of cross layers
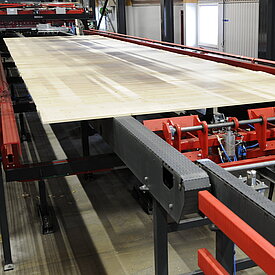
Transport of pressed CLT elements
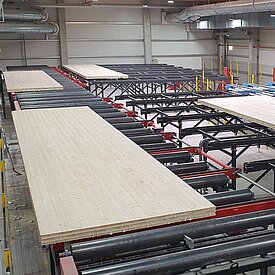
Lifting table for transport into the upper floor
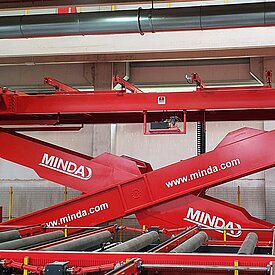
Driving portal for glue application
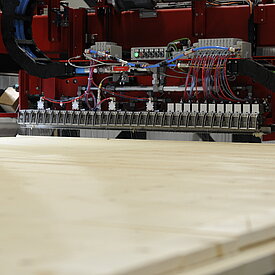
Laying areas in front of two CLT presses
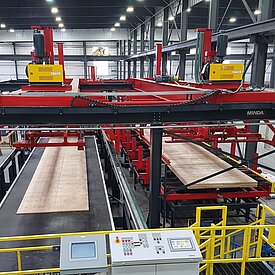
Push-off station
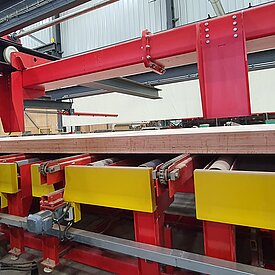
Buffer for cross layers
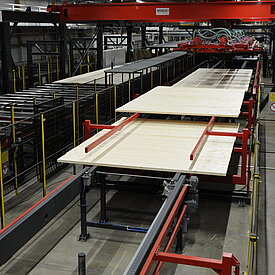